You are wondering how Metalu Plast designs its projects? What are our validation and testing steps? How the Metalu Plast products go from prototype to manufacturing? Would you like to discover the backstage of the leading French manufacturer of sports equipment? We will tell you all about the manufacturing process of Metalu Plast in 5 steps!
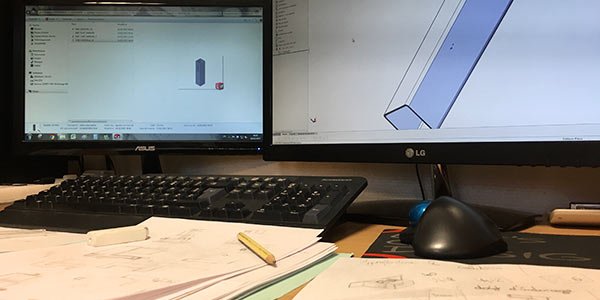
Step 1 – The analysis, a key step
We take the time to review each of your comments, the observations made to our commercial team or through our client support service and the remarks submitted during commercial workshops, fairs or in the field. We use this feedback to properly understand your needs and the final users requirements in order to determine:
- Who is the final user of our equipment, what are his profile and behaviour?
- What are his actual needs?
- What are the main functions of our sport installations?
- Under which environment these facilities are going to be used?
The answers we gathered enable us to write a design brief, allowing our engineering office to work on new innovations following our continuous improvement processes.
Step 2 – The study: define the best solutions
The engineering office and the managers analyse the best answer to the identified needs among all the different propositions made and its manufacturing cost. Afterwards, the product is modelled in 3D to get an insight of:
- Parts to be manufactured
- Parts to buy (with a consultation and an approval of the purchasing department)
- Miscellaneous item to take into account for the manufacturing of the product (packing, shipping)
Once the template is approved by the management, a prototype must be manufactured to test the product in real life conditions.
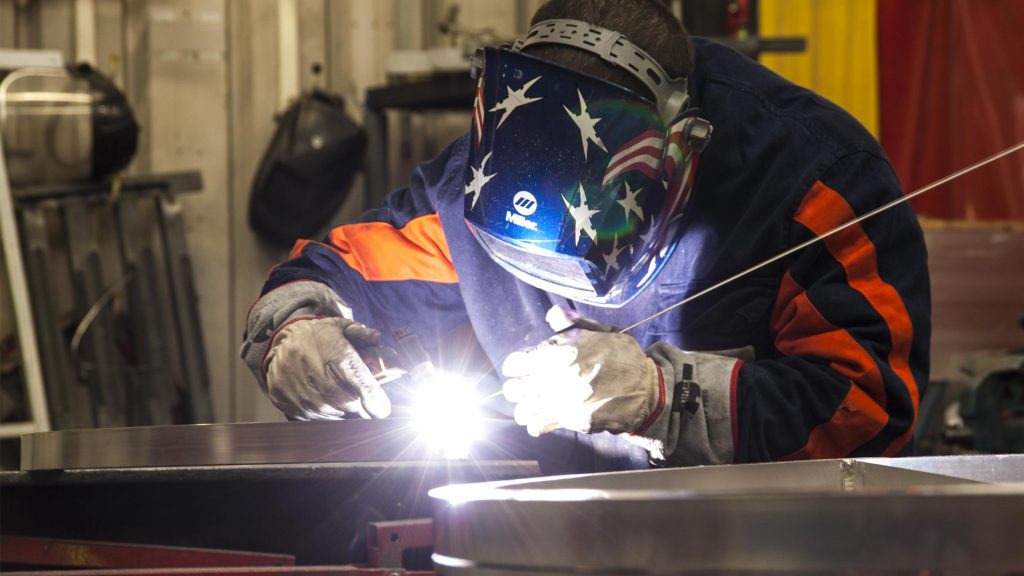
Step 3 – The prototyping: the iteration principle
A prototype is manufactured and assembled by our team. This prototype will be tested with certified processes and real life tests. If the testing phase isn’t satisfying enough, we re-build new prototypes until we get an optimum level of quality and security for a product that best answers your needs and conforms to standards. This iterative process that could last for hundreds of hours is the key to a successful manufacturing process. For example, the design, testing and modelling steps of our dB-Lock flange for handrails required more than 1300 hours of work before reaching the recommended level of quality.
Step 4 – The manufacturing and further testing
With the tests satisfactorily passed, the product is industrialized. This step is crucial and requires to perfectly handle the supply and the manufacturing of the products’ parts as well as the synchronization of all the activities of the factory: cutting, drilling, welding, shot blasting, plastic-coating, packing… Simultaneously, we create the technical documents that will be provided to you (technical manuals, installation procedures and other information that you may need while using the product). Finally, further testing is performed by an independent agency to ensure the product you receive is compliant with the standards.
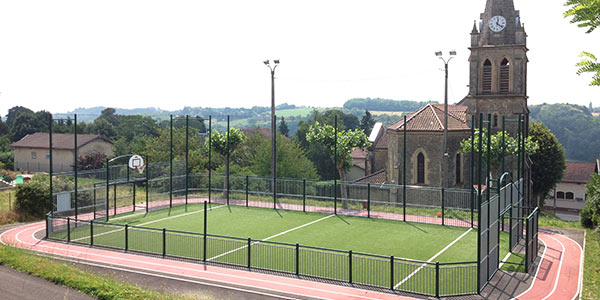
Step 5 – The product launch
This step is the tip of the iceberg. From there on, we will proceed with the following steps together through custom-made projects that best answer your needs!
Of course, our sales team is at your disposal for any further information and offers you support all along your project at 00 2 31 23 22 00.